In actual production, for the processing of RaO.04μm~Ra1.6μm inner hole with surface roughness, the common processing technologies are grinding, rolling, broaching and honing.
Broaching tools are expensive, efficient and suitable for mass production. The roughness of honing surface for finishing requires Ra0.04 um or more. So grinding and rolling are commonly used. Next, through the analysis of the processing technology of a part, the grinding and rolling processes are compared.
The parts are shown as follows: the inner diameter isφ140±063, the roughness is Ra0.08μm, and the roundness tolerance is 0.045 mm.
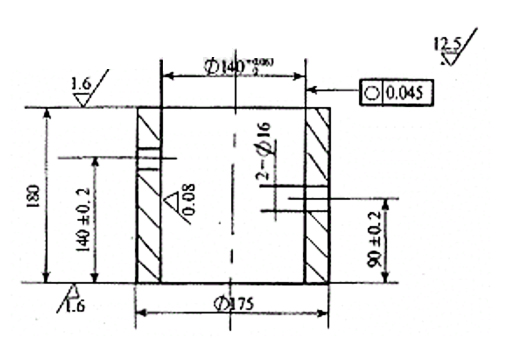
Internal hole grinding, rolling burnishing, internal hole processing technology, advantages of rolling burnishing, disadvantages of rolling burnishing, advantages of grinding, shortcomings of grinding, roller burnishing tools manufacturers, use of roller burnishing tools, improve the dimensional accuracy of parts, reduce surface roughness, customize roller burnishing tools
The original processing technology: turning–Rough grinding–finish grinding. Turning residual grinding is 0.2mm~0.4mm. This process can ensure the technical requirements of the processed parts. Field test results show that the surface roughness Ra is 0.08 μm, the dimension is within the tolerance range of φ140~φ140±063 mm, and the roundness tolerance is within the range of 0~0.025 mm. Grinding is a high-speed cutting, which can be dispersed, reduce the surface roughness of parts, and improve the dimensional accuracy and geometric accuracy of parts.
But he still has many shortcomings: 1. In the grinding process, because of the rapid grinding speed, a large amount of grinding heat will be transferred to the parts, which makes the parts temperature rise tens of degrees, the parts shrink after cooling (affected by ambient temperature), and the aperture shrink. In order to ensure the dimensional accuracy, the workpiece size after completion needs to be adjusted artificially, so there will be the phenomenon of inaccurate processing size. 2. The high temperature in the grinding zone (the local surface temperature can reach 1000 C) causes great harm to the service performance of the parts. The surface layer will have residual tensile stress, grinding cracks, burns and so on. 3. In actual production, it is difficult to reduce the heat generated by grinding and the grinding efficiency is low.
Current processing technology: roughing–half finishing turning –finish turning– roller burnishing. Parts can be processed on the lathe, and this process can also fully guarantee the technical requirements of parts. Field results show that the surface roughness is Ra0.08 μm, the dimension is between φ140.02 mm – φ140.04 mm, the processing dimension is relatively concentrated, and the roundness tolerance is between 0.01 and 0.03. In order to ensure the quality of the parts, the process requires a high turning requirement. The surface roughness of the finished parts is Ra3.2μm and the dimension is φ140-0.01 0.02. Because the actual pressing volume of the parts processed by rolling is very small and the parts are processed by positioning themselves on the surface of the parts processed, the surface roughness of the parts can be reduced and the dimensional accuracy can be improved. However, the shape deviation of parts will not be significantly improved, so the accuracy of parts after rolling mainly depends on the accuracy of pre-processing (turning) and surface roughness before rolling. Rolling processing is chip-free processing, no heating phenomenon, and the finished size, i.e. the forming size, is easy to control. Residual compressive stress and cold hardening are produced on the surface of parts by rolling, which can improve the fatigue strength of parts, and its production efficiency is high. The disadvantage of this method is the need to customize roller burnishing tools. We are a manufacturer of roller burnishing tools. If you need custom roller burnishing tools, you can send drawings of processed parts to consult us.
The inner hole grinding process and rolling burnishing process can improve the dimensional accuracy and reduce the surface roughness. But there are the following differences:
The requirement of inner hole grinding is not high, which can reach higher precision than rolling machining. In the actual production, it is difficult to reduce the temperature of the grinding area in the process of inner hole grinding, and the residual tensile stress, grinding cracks and burns will be generated in the processing of surface layer, which will affect the service performance of parts and lead to low production efficiency.
Rolling burnishing has high requirements for the previous process and cannot improve the shape accuracy of parts. Because there is no heating in the processing process, it is easy to control the residual compressive stress and cold hardening in the surface layer of parts processing, which is conducive to improve the service performance of parts and high production efficiency.