Tool and machine tool are interdependent relationship, there is no tool tool is not complete. The machine tool is the tool processing work piece carrier. The basic requirement of tool use is not only to match the base of installation, but also to match the workpiece to be processed. Shape matching and size matching are the basic conditions for the tool to be installed on the machine tool. But this is only the most basic part of the machine tool installation tool is to use the tool to complete specific processing tasks. The matching between the cutter and the workpiece processed contains many contents. The tool tip is an important part of the tool, is the tool and the workpiece contact the most commonly used point, but also the most important point. The cutting performance of the tool tip is affected by three factors, that is, the matrix material characteristics, the surface shape of the tool tip and the geometric shape of the tool tip. The degree of cooperation among the three determines the interaction between them, and thus determines the performance of the tip. The matrix material bears most of the cutting force and heat during the machining process. Nowadays, matrix materials are divided into many types, among which cemented carbide is the most frequently used one. Take tungsten-base cemented carbides as an example. In tungsten-cobalt cemented carbides, the higher the cobalt content in the matrix, the stronger the impact resistance will be. And the harder the matrix contains tungsten carbide, the higher the hardness. It is because of the characteristics of the matrix material in the processing, if the impact is small, can choose the matrix material containing less cobalt carbide tool, the tool will have good wear resistance. If the impact is larger, the matrix material can be used to contain higher cobalt content of cemented carbide tool, the tool hardness is high, can effectively prevent the process of breaking the state of the tool.
Category Archives: RBT News
Here are the newest technical articles, videos and pictures of Roller Burnishing Tools, we focus on mirror surface finishing and technology sharing.
Introduction of American brand cutting tools
-
Kennametal
Kennametal was created in 1938. America, metallurgists Philip M.M Kenna after years of painstaking research, invented a tungsten – titanium carbide alloy tool new material, can make the machining efficiency of cutting steel get breakthrough improvement. Based on this invention, Philip founded McKenna Metals Company in Latrobe, Pennsylvania, which was renamed Kennametal. Nowadays, Kennametal has developed into a large multinational corporation with world leading level in cutting tools, tool systems, new materials and technical services.
-
Onsrud
Onsrud – American aviation cutter expert The company specializes in manufacturing aluminum, plastics and composites in the aerospace industry. Onsrud is a leading technology company specialized in manufacturing high performance carbide /PCD/CBN reamer, high precision groove milling cutter and integral carbide end milling cutter for aluminum alloy and plastics processing.
-
MasterCut
MasterCut Tool is a company that manufactures hard alloy cutting tools. Its main products include: end mills for CNC machine tools, machining centers, various types of carbide rotary files, etc. Cutting king in the United States is known for its high precision, long life and high market share.
-
MILLSTAR
MILLSTAR is a well-known American mold and tool manufacturer with decades of cutting tool manufacturing experience. Its products are mainly used in the mold manufacturing, aerospace, electric power and medical equipment industries.
-
SGS
SGS has been immersed in the technology of solid carbide rotary cutting tools for many years, and its business covers aerospace, medical equipment, energy power and automobile industry. The company has established manufacturing bases in the United States and the United Kingdom, and its products are sold to more than 60 countries and regions. In April 2016, KYOCERASGS corporation signed the equity transfer agreement with SGS Tool Company, a manufacturer of integrated Tools in the United States. The equity of SGS Tool Company and its group Company will be transferred to kyocera, renamed as KYOCERASGS Precision Tools, Inc, and officially became a wholly-owned subsidiary of kyocera.
How to deal with the rancidity of cutting fluid?
Due to its good cooling and lubrication performance, excellent operating environment and low production cost, water-soluble cutting fluid is favored by many machining customers and occupies a high proportion in the current market application. However, due to the characteristics of its own products, many problems will appear in daily use, especially the problem of deterioration and odor, causing headaches for many customers.
Why does the workshop stink?
Cutting fluid metamorphism refers to oxygen consuming bacteria living in a mineral environment, such as water, concentrate of cutting fluid and oil leaking from machine tools, splitting into two parts every 20 to 30 minutes under aerobic conditions. Anaerobic bacteria, on the other hand, live in an oxygen-free environment, and divide into two parts per hour. The metabolism releases SO2, which smells of rotten eggs and darkens the cutting fluid. When the bacteria in the cutting fluid is greater than 106, the cutting fluid will stink.
Bacteria enter the cutting fluid mainly through the following channels:
- Bacteria invade during preparation, as in the water in which cutting fluids are prepared.
- Bacteria from the air enter the cutting fluid.
- The transfer of the workpiece between processes results in an infection of the cutting fluid.
- The operator’s bad habits, such as littering.
- Poor cleanliness of machine tools and workshops.
Methods of controlling bacterial growth:
- Use high quality and stable cutting fluids.
- When the concentrate is prepared with pure water, it is not only easy to prepare, but also improves the lubricity of the cutting fluid, reduces the amount taken away by chips and prevents bacterial erosion.
- When used, control the concentration ratio of the cutting fluid should not be too low, otherwise the bacteria can easily grow.
- As the oil used by the machine tool contains bacteria, it is necessary to minimize the oil leakage from the machine tool into the cutting fluid.
- When the pH value of cutting fluid is between 8.3 and 9.2, the bacteria cannot survive, so new cutting fluid should be added in time to increase the pH value.
- Keep the cutting fluid clean and do not allow it to come into contact with dirt such as oil, food and tobacco.
- Use fungicides frequently.
- Keep workshop and machine tools clean.
- If there is no filter equipment, the equipment should be regularly skimmed to remove oil slick, dirt removal.
What is CNC polishing, and how to polish?
Polishing refers to the processing method that makes the surface roughness of the workpiece reduced by mechanical, chemical or electrochemical actions to obtain a bright and smooth surface. It is the use of polishing tools and abrasive particles or other polishing media on the surface of the workpiece modified processing.
How to polish?
- Mechanical polishing
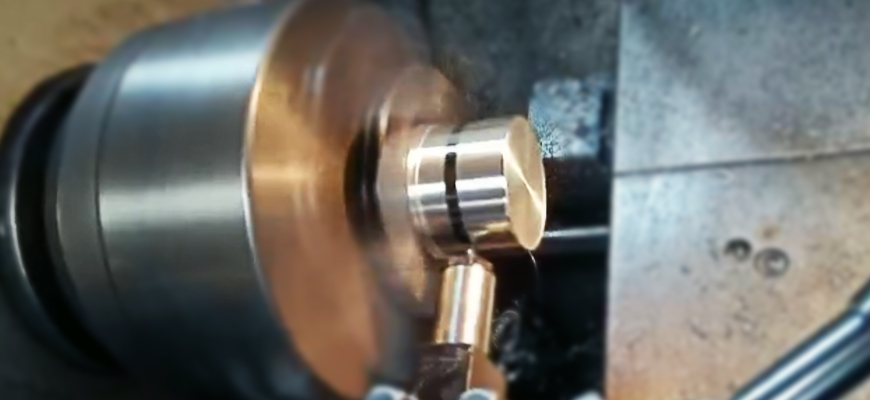
Diamond Burnishing Tools Manufacturer, Supplier, Wholesaler & Exporter
Mechanical polishing is a method of polishing a smooth surface by cutting or plastic deformation of the material surface to remove the convex part after being polished. Mechanical polishing generally USES the whetstone bar, wool wheel, sandpaper, and so on, mainly manual operation. Special parts, such as the surface of the rotary body, can be used by the turntable and other auxiliary tools. The workpiece with high surface quality may adopt the method of super fine grinding and polishing. Ultra-fine grinding and polishing is a special grinding tool. In the grinding and polishing liquid containing abrasive materials, it is pressed on the surface of the workpiece being processed for high-speed rotational motion. Surface roughness of Ra0.008μm can be achieved by using this technology. This method is the highest of all polishing methods. This method is often used in optical lens mould.
- Chemical polishing
Chemical polishing is to make the surface of the material in the chemical medium surface protruding part than the concave part of the first dissolution, so that smooth surface. The main advantage of this method is that it does not require complex equipment and can polish the workpieces with complex shapes, and many workpieces can be polished at the same time. It works efficiently. The key problem of chemical polishing is the preparation of polishing liquid. The surface roughness obtained by chemical polishing is generally 10μm.
- Electrolytic polishing
The basic principle of electrolytic polishing is the same as chemical polishing, that is, the surface of the selectively dissolved material is slightly protruding to make the surface smooth. Compared with chemical polishing, the effect of cathode reaction can be eliminated and the effect is better.
The electrochemical polishing process is divided into two steps:
(1) macro leveling
The solution diffuses into the electrolyte, the surface of the material decreases geometrically, Ra>1μm.
(2) slightly smooth
Anode polarization, increased surface brightness, Ra<1μm.
- Ultrasonic polishing
The workpiece is put into the abrasive suspension and put together in the ultrasonic field, and the abrasive is ground and polished on the surface of the workpiece by the ultrasonic oscillation. The macroscopic force of ultrasonic machining is small, which will not cause deformation of workpiece. Ultrasonic machining can be combined with chemical or electrochemical methods. On the basis of solution corrosion and electrolysis, ultrasonic vibration is applied to stir the solution to separate the dissolved product on the surface of the workpiece, and the corrosion or electrolyte near the surface is even.
- Fluid polishing
Fluid polishing depends on the high-speed flow of the liquid and its carrying abrasive particles to flush the surface of the workpiece to achieve the purpose of polishing. Common methods are: abrasive jet machining, liquid jet machining, fluid power grinding, etc.
- Magnetic grinding and polishing
Magnetic grinding and polishing is to use magnetic abrasive under the action of magnetic field to form abrasive brush, grinding the workpiece. This method has high efficiency, good quality and easy control of processing conditions. With suitable abrasive, the surface roughness can reach Ra0.1μm.