Skive and Roller Burnishing Tool is also called boring and rolling tool, scraping and rolling tool, oil cylinder scraping and rolling tool, etc. With advanced boring and rolling combined processing technology in Europe, the boring and rolling function can be completed once and again. The processing accuracy can reach IT8 level and the surface roughness can reach Ra005-0.2 micron. Skiving and Roller burnishing Tool is mainly used for finishing the inner hole of hydraulic cylinder. Compared with the traditional honing machine, the equipment has the advantages of low noise and pollution-free, and can greatly save labor costs and high processing efficiency. Hydraulic Cylinder Finishing Tool can save 80-90% of the processing time than the old boring rolling or boring honing.
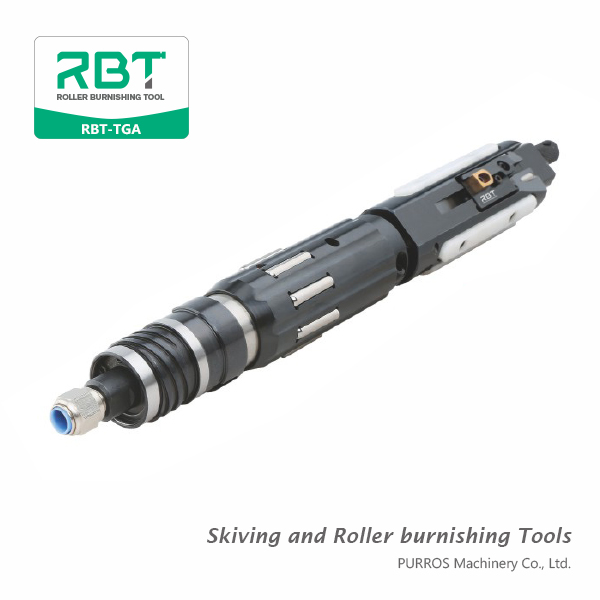
RBT Skiving and Roller burnishing Tools, Skiving and Roller burnishing Tools, Skiving burnishing Tools, Roller burnishing Tools, Skiving burnishing Tools Manufacturer, Skiving burnishing Tools for Sale, Skiving burnishing Tools Supplier, Deep Hole Burnishing Tool, Skiving and Roller burnishing Tools for Oil Cylinder
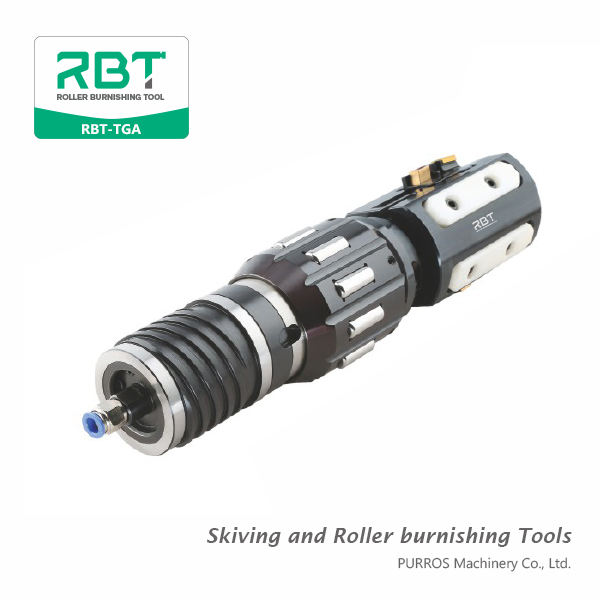
Skiving and Roller burnishing Tools, Skiving burnishing Tools, Roller burnishing Tool, RBT Roller burnishing Tool, Skiving and Roller burnishing Tool Manufacturer, Skiving and Roller burnishing Tool Supplier, Skiving and Roller burnishing Tool for Sale, Cheap Skiving and Roller burnishing Tool, Cutting And Roller Burnishing for Inner Surfaces, Deep Hole Burnishing Tool, Skiving and Roller burnishing Tools for Oil Cylinder
Main features of Skive and Roller Burnishing Tool:
- To improve the surface roughness, the roughness can basically reach about Ra ≤0.08 M.
- Correct roundness, the ellipticity can be less than 0.01 mm.
- Increasing surface hardness, eliminating stress and deformation, and increasing hardness HV≥4°.
- There is residual stress layer after processing, and the fatigue strength is increased by 30%.
- Improve the quality, reduce wear and tear, prolong the service life of parts, but reduce the processing cost of parts.