Both the internal hole grinding process and rolling finishing process can improve the dimension accuracy of parts and reduce the surface roughness. But there are the following differences:
The internal hole grinding has not high requirements for the upper process, and can achieve higher precision than the rolling process. In actual production, it is difficult to reduce the temperature of grinding area in the process of inner hole grinding, and the residual tensile stress, grinding cracks and burns generated in the surface layer will be generated. These can affect the performance of parts and make the production efficiency low.
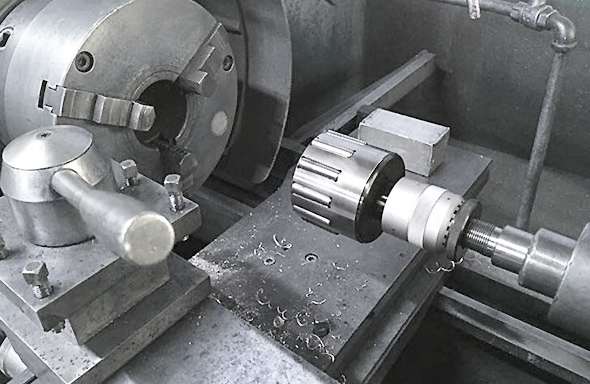
Rolling Machining
The rolling process has high requirements on the upper process, which cannot improve the shape accuracy of parts. The size is easy to control because there is no heating in the process. The residual compressive stress and cold hardening produced by the surface layer of parts can improve the performance of parts. It is highly productive.